In-depth Guide to Compactor Maintenance
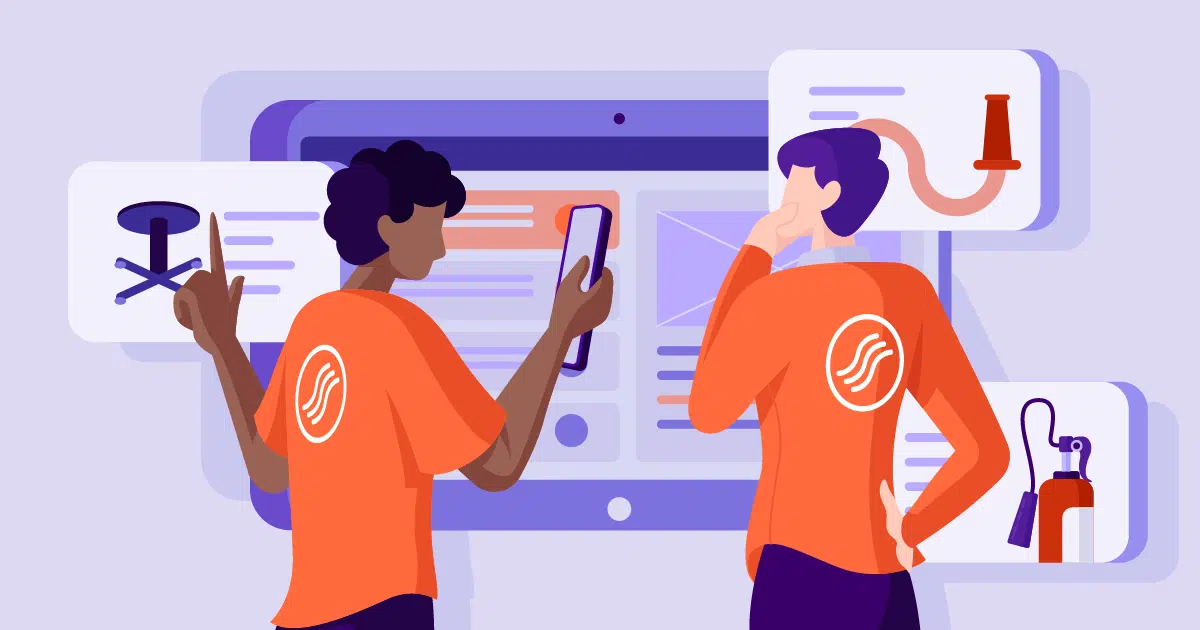
Welcome to our ultimate guide on compactor maintenance! In this blog, we’ll dive into the world of compactors, addressing the pain points the industry faces when it comes to keeping these machines in top shape. Whether you’re a construction pro, waste management expert, or just curious about compactor care, we’ve got you covered.
Compactors are vital equipment used in various industries to reduce waste volume, improve efficiency, and promote a cleaner environment. However, neglecting maintenance for your commercial trash compactors, recycling equipment, or general waste compactor leads to shorter lifespans, decreased productivity, higher repair costs, and safety risks.
Throughout this blog, we’ll tackle common challenges like identifying issues, establishing maintenance routines, and training staff. By addressing these pain points, we’ll equip you with the knowledge to keep your compactors running smoothly and efficiently.
We understand that each industry has unique compactor maintenance needs. Whether you’re dealing with large-scale landfill compactors or smaller models for recycling facilities, we’ll provide tailored insights.
Keep reading to find out how civil management software can help you.
Understanding Key Components of a Compactor
Let’s dig into the essential components of a compactor that demand regular maintenance. These components play vital roles in the overall operation of the compactor, ensuring its optimal performance and longevity. Here are the key components to focus on:
Engine:
The engine is the powerhouse of the compactor, responsible for generating the necessary power to drive the machine. Regular maintenance of the engine involves checking and changing oil, inspecting and replacing filters, and ensuring proper fuel quality. A well-maintained engine ensures efficient operation and prevents breakdowns during critical tasks.
Hydraulic System:
The hydraulic system of a compactor controls various functions, such as the compaction plate, loading mechanisms, and container ejection. Maintenance tasks for the hydraulic system include monitoring hydraulic fluid levels, checking for leaks, inspecting hoses and seals, and ensuring proper pressure. Regular maintenance ensures smooth and reliable operation, preventing costly hydraulic failures.
Compacting Mechanism:
The compacting mechanism, typically a plate or drum, is responsible for compressing waste materials. Regular maintenance involves inspecting the compaction surface for wear and damage, lubricating moving parts, and ensuring proper alignment. Well-maintained compacting mechanisms guarantee optimal compaction performance, reducing waste volume effectively.
Electrical Systems:
Electrical systems control various components of the compactor, including sensors, safety features, and controls. Regular maintenance involves inspecting electrical connections, checking for loose wires, and ensuring proper functioning of switches and sensors. Proper maintenance of electrical systems promotes safe and reliable operation while minimising the risk of electrical failures.
Each of these components plays a crucial role in the compactor’s overall operation. The engine provides the necessary power to drive the machine and ensures efficient performance. The hydraulic system enables precise control over compaction and loading functions, enhancing productivity. The compacting mechanism compresses waste materials, maximising waste volume reduction. Lastly, the electrical systems ensure safe and reliable operation, controlling critical functions and enhancing operator safety.
By regularly maintaining these components, you can optimise the compactor’s performance, extend its lifespan, minimise downtime, and reduce repair costs. Implementing a proactive maintenance routine for these crucial components is key to ensuring the compactor operates at its best, maintaining productivity and delivering efficient waste management solutions.
Daily Maintenance Checks for Compactors
Performing daily maintenance checks is crucial to prevent potential breakdowns and ensure the smooth operation of the compactor. These routine checks help identify issues early on, allowing for timely repairs and minimising costly downtime. Here are the main checks that should be performed daily before using the compactor:
Inspect for leaks: Check for any signs of hydraulic, fuel, or coolant leaks. Addressing leaks promptly prevents fluid loss and potential damage to components.
Ensure correct fluid levels: Check and maintain proper levels of hydraulic fluid, engine oil, coolant, and fuel. Inadequate fluid levels can lead to poor performance and increased wear on the components.
Check for wear and tear: Inspect the compacting mechanism, such as the plate or drum, for any signs of wear, damage, or misalignment. Also, examine hydraulic hoses, belts, and other mechanical parts for wear or deterioration.
Examine filters: Inspect and clean or replace filters as needed. Clogged filters can restrict fluid flow and reduce the efficiency of the compactor.
Test safety features: Verify that all safety features, such as emergency stops and warning alarms, are in proper working condition. Ensure that safety guards and covers are intact.
Check electrical connections: Inspect electrical connections, wiring, and switches for any loose connections or signs of damage. Faulty electrical systems can pose safety hazards or lead to operational issues.
Lubrication: Apply lubrication to moving parts as recommended by the manufacturer. Adequate lubrication reduces friction and extends the lifespan of components.
Verify controls and gauges: Test and ensure that all controls, gauges, and indicators are functioning properly. This includes checking instrument panels, pressure gauges, and operational controls.
Clean the compactor: Keep the compactor clean from debris, dust, and waste accumulation. This helps prevent clogging, corrosion, and potential damage to sensitive components.
By conducting these daily maintenance checks, you can identify any potential issues, address them promptly, and maintain the optimal performance of the compactor. This proactive approach minimises the risk of breakdowns, enhances safety, and extends the lifespan of the equipment.
Periodic Maintenance for Compactors
Periodic maintenance tasks are essential to ensure the efficient operation and longevity of compactors. These tasks go beyond daily checks and involve more in-depth inspections and servicing. Here are the different types of maintenance tasks that should be performed periodically:
Filter changes: Regularly change filters, such as hydraulic filters, oil filters, and fuel filters, based on the manufacturer’s recommendations or when they become clogged. Clean filters improve fluid flow, prevent contamination, and enhance component performance.
Lubrication: Apply lubrication to moving parts, such as bearings, chains, pivot points, and slide rails, as specified by the manufacturer. Lubrication reduces friction, minimises wear and tear, and ensures smooth operation.
Belt tension adjustment: Check and adjust the tension of belts in the drive system. Proper belt tension helps maintain efficient power transmission and prevents slippage or premature wear.
Wear and tear inspection: Thoroughly inspect components for wear, damage, or signs of deterioration. This includes inspecting the compaction surface, hydraulic hoses, seals, belts, and other critical parts. Addressing wear and tear promptly prevents further damage and maintains optimal performance.
Electrical system inspection: Inspect electrical connections, wiring, switches, and control panels for any signs of damage, corrosion, or loose connections. Test safety features, controls, and gauges. Addressing electrical issues ensures safe and reliable operation.
System pressure checks: Periodically check and adjust hydraulic system pressure as recommended by the owner’s manual. Proper pressure levels optimise compaction performance and prevent unnecessary strain on components.
Belt and chain tension inspection: Inspect and adjust the tension of belts and chains in the drive system. Proper tension ensures efficient power transmission and reduces wear.
Component alignment: Verify and adjust the alignment of the compaction plate or drum to ensure proper contact and uniform compaction. Misalignment can lead to uneven compaction and reduced efficiency.
The frequency of these maintenance tasks may vary depending on the manufacturer’s recommendations, operating conditions, and usage intensity. Generally, periodic maintenance is performed on a monthly, quarterly, or annual basis. Adhering to the recommended maintenance schedule is vital for the efficient operation of compactors, as it helps prevent unexpected breakdowns, reduces the risk of costly repairs, and extends the overall lifespan of the equipment.
Cleaning and Proper Storage of Compactors
Proper cleaning and storage are crucial for compactor maintenance. Cleaning removes debris and corrosive substances, prolonging component lifespan and ensuring optimal performance.
For storage, choose a dry, well-ventilated location away from extreme temperatures and moisture. Secure movable parts, follow manufacturer guidelines, and ensure the compactor is dry before storing. These practices prevent corrosion, damage, and potential issues, maximising the compactor’s lifespan and performance.
The Role of Maintenance Records in Compactor Upkeep
Maintaining comprehensive maintenance records is crucial for effective compactor maintenance. These records provide a valuable reference for tracking maintenance history, identifying trends, and planning future tasks.
To create and manage an effective maintenance log, document all maintenance activities, include relevant information like model and serial numbers, track maintenance schedules, note any issues or abnormalities, record technician details, utilise digital tools if possible, and regularly review and analyse the log.
By keeping thorough records, compactor operators can optimise maintenance strategies and ensure long-term reliability.
Dealing with Common Compactor Maintenance Issues
Compactors can experience various maintenance issues, including poor compaction performance, fluid leaks, unusual noises or vibrations, electrical malfunctions, and hydraulic system problems.
To address these issues, operators should inspect and adjust settings, replace worn-out parts, tighten connections, and troubleshoot electrical or hydraulic components. However, if problems persist or require specialised expertise, it’s advisable to seek professional assistance.
Professional technicians can diagnose complex issues, provide proper repairs, and ensure the compactor’s long-term performance and safety. Ensure that you have proper operation with regular preventative maintenance for your trash compactor.
The Importance of a Preventive Maintenance Program for Compactors
The benefits of a preventive maintenance program for compactors are significant and can greatly contribute to the efficient operation and longevity of the equipment. Here are the key benefits of implementing a preventive maintenance program:
Minimise downtime: Regular maintenance helps identify potential issues before they cause major breakdowns, reducing unplanned downtime and maximising the compactor’s availability for operation.
Reduce repair costs: Addressing minor problems early through preventive maintenance prevents them from escalating into major, costly repairs. This saves money on emergency repairs and replacement of critical components.
Extend equipment lifespan: Proper maintenance ensures that the compactor operates within optimal parameters, reducing wear and tear on components and extending the overall lifespan of the equipment.
Optimise performance: Regular inspections, lubrication, and adjustments maintain the compactor’s performance at peak levels, ensuring efficient waste compaction and minimising energy consumption.
Enhance safety: A well-maintained compactor reduces the risk of safety incidents caused by faulty components or systems, providing a safer working environment for operators and other personnel.
To establish an effective preventive maintenance program for compactors, consider the following key elements:
Create a maintenance schedule: Develop a comprehensive schedule outlining routine maintenance tasks, including daily, weekly, monthly, quarterly, and annual checks. This ensures that all necessary maintenance activities are performed consistently.
Document maintenance procedures: Create detailed guidelines for each maintenance task, including step-by-step instructions, recommended tools, and safety precautions. This documentation helps maintain consistency and assists maintenance personnel in performing tasks accurately.
Train maintenance personnel: Provide training to maintenance staff on proper maintenance procedures, safety protocols, and equipment-specific requirements. Well-trained personnel are more capable of identifying potential issues and performing maintenance effectively.
Maintain accurate records: Keep detailed records of maintenance activities, including dates, tasks performed, parts replaced, and observations made. These records provide a valuable reference for tracking maintenance history, identifying trends, and planning future maintenance tasks.
Regularly review and update the program: Periodically evaluate the effectiveness of the preventive maintenance program. Make adjustments as needed based on feedback from maintenance personnel, equipment performance, and evolving industry best practices.
By implementing a preventive maintenance program, compactor operators can proactively manage maintenance tasks, prevent costly breakdowns, optimise performance, and extend the overall lifespan of the equipment. The program provides a structured approach to maintenance, ensuring that essential tasks are consistently performed and maximising the compactor’s efficiency and reliability.
Safety Considerations in Compactor Maintenance
Safety during maintenance activities is paramount to prevent accidents and injuries. Establishing a safety-oriented culture in maintenance operations leads to better maintenance outcomes and reduces the risk of accidents.
By prioritising safety, organisations can ensure compliance with regulations, enhance productivity, improve morale and retention, promote continuous improvement, provide training and awareness, and demonstrate leadership commitment.
A safety-oriented culture protects personnel, creates a positive work environment, and contributes to the overall success of maintenance operations.
Introducing FieldInsight for Compactor Maintenance
When it comes to selecting the ultimate service management software, there is truly only one choice that stands out from the rest. FieldInsight is the all-in-one platform that ticks all the boxes for your business needs and beyond. With its unparalleled flexibility, customizability, and scalability, FieldInsight is designed to seamlessly integrate into your operations without any hassle. Say goodbye to juggling multiple software solutions and welcome a comprehensive platform that covers everything you require.
FieldInsight’s extensive array of features is unparalleled in boosting your business’s productivity. From scheduling and inventory management to GPS tracking, invoicing, customer communication, notifications, asset management, and much more – FieldInsight has got you covered. Gain full control over your projects, track materials, view infrastructure plans, and ensure efficient preventative maintenance. Enforce guidelines set by your supervisors, streamline equipment maintenance, and witness your business thrive like never before.
What sets us apart is not just our cutting-edge features but also our commitment to your success. We prioritise your satisfaction by offering a seamless implementation process where our experts guide you every step of the way. We understand that transitioning to a new software can be daunting, which is why we provide dedicated support and ensure you’re comfortable and confident in utilising our software. Moreover, as an Australian-based field service management software, we constantly strive to enhance the customer experience, consistently improving and growing to meet your evolving needs.
Don’t settle for mediocrity when you can have excellence with FieldInsight. Experience the power of a comprehensive service management software that’s designed to propel your business forward. Choose FieldInsight and unlock your business’s true potential.
For your heavy equipment maintenance, from the oil filter, power unit, to grease fittings, ensure that you never miss a step with a field service software at your back.
Conclusion
In conclusion, maintaining compactors is not just a necessity but a strategic investment for businesses in the waste management industry. By implementing a proactive maintenance approach, compactor operators can reap numerous benefits.
Regular maintenance checks, both daily and periodic, help identify potential issues, prevent breakdowns, and ensure the compactor operates at its best. A preventive maintenance program minimises downtime, reduces repair costs, extends equipment lifespan, and optimises performance. Furthermore, emphasising a safety-oriented culture during maintenance activities is crucial to protect personnel, enhance productivity, and foster a positive work environment.
By prioritising maintenance and safety, compactor operators can maximise efficiency, reduce accidents, and achieve long-term success in their waste management operations.
Book a chat with one of our sales members to discuss how we can help you today.
What You Should Do Now
- Book a Demo. You’ll be in touch with an automation expert who has worked in this space for over 5 years, and knows the optimal workflow to address your needs.
- If you’d like access to free articles about managing HVAC workflows, go to our blog.
- If you know someone who’d enjoy reading this page, share it with them via email, Linkedin, Twitter, or Facebook.