Comprehensive Guide to Drilling Rig Maintenance
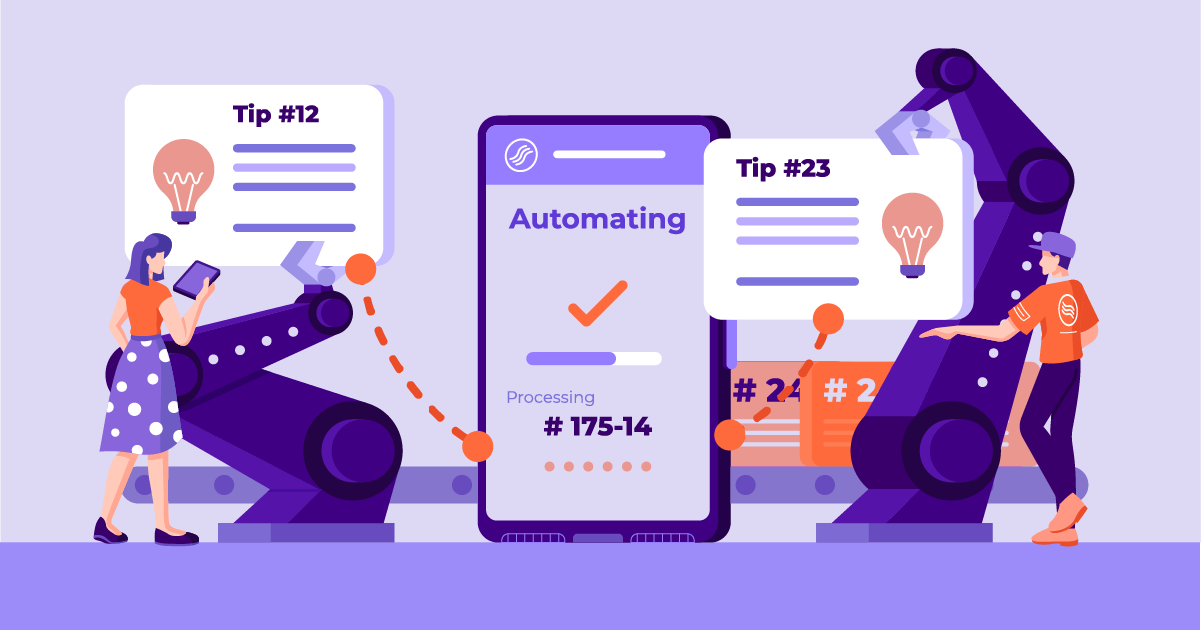
Maintaining drilling rig equipment is of paramount importance to ensure safe and efficient operations in the oil and gas industry. If you work in the drilling industry, you understand the need for a proper maintenance schedule and how hard it can be to manage all the moving parts.
This comprehensive guide will provide valuable insights into the various aspects of drilling rig maintenance, covering crucial components, daily maintenance checks, routine and preventive maintenance, cleaning and storage, documentation, common maintenance issues, implementing a preventive maintenance program, safety considerations, and the introduction of FieldInsight, a cutting-edge civil management software.
By following the recommendations in this guide, you can optimize the performance of your drilling rig, extend its lifespan, and minimize downtime. Gain control of your business with civil management software today.
Understanding the Crucial Components of a Drilling Rig
A drilling rig comprises several key components, each playing a vital role in its overall operation. Regular maintenance of these components is essential to prevent breakdowns and ensure the efficient functioning of the rig. The key components requiring regular maintenance include:
- Hoisting Equipment: The hoisting equipment is responsible for lifting and lowering heavy loads during drilling operations. Regular inspections and maintenance are crucial to prevent equipment failure and ensure the safety of personnel.
- Drill Rods: Drill rods are essential for transmitting power and torque to the drill bit. Regular inspection and maintenance of drill rods help identify and replace worn-out or damaged sections, ensuring the integrity of the drilling process.
- Mud Circulation System: The mud circulation system is responsible for cooling and lubricating the drill bit, carrying cuttings to the surface, and maintaining pressure control. Regular maintenance, including cleaning, monitoring fluid levels, and replacing filters, is essential for the system’s optimal performance.
- Drill Bits: Drill bits are subject to significant wear and tear during drilling operations. Regular maintenance involves inspecting for damage, sharpening or replacing worn-out bits, and ensuring proper alignment to maximize drilling efficiency.
- Engine: The engine powers the drilling rig and drives various components. Regular maintenance, including oil and filter changes, inspections for leaks or malfunctions, and monitoring fuel efficiency, helps prevent unexpected breakdowns and ensures the engine’s longevity.
- Hydraulics: Hydraulic systems are responsible for operating various components of the drilling rig, such as the draw works and pipe handling systems. Regular maintenance, including checking fluid levels, inspecting hoses and seals for leaks, and ensuring proper hydraulic pressure, is essential for smooth rig operations.
- Filters: Filters play a critical role in maintaining clean fluids in the drilling rig, preventing damage to components. Regular replacements of filters, based on manufacturers’ recommendations, help ensure optimal filtration and extend the lifespan of equipment.
- Hoses: Hoses are essential for transferring fluids and maintaining proper pressure within the drilling rig. Regular inspection and replacement of hoses help prevent leaks, ensure safety, and maintain efficient operations.
Benefits of Daily Drilling Equipment Maintenance Checks
Performing daily equipment maintenance checks before using the drilling rig is a proactive measure to identify potential malfunctions and prevent accidents. The benefits of conducting these checks include:
- Early Detection of Issues: Daily maintenance checks help identify issues at an early stage, allowing for timely repairs and minimizing the risk of equipment failure during operation.
- Enhanced Safety: By identifying and addressing potential safety hazards, daily maintenance checks contribute to a safer working environment for rig personnel.
- Cost Savings: Preventive maintenance can save significant costs by addressing minor issues before they escalate into major problems, avoiding costly repairs and downtime.
Daily maintenance checks should include:
- Inspecting for Leaks: Check all components for signs of leaks, such as fluid drips or stains. Pay particular attention to hydraulic lines, connections, and valves.
- Checking Oil and Fluid Levels: Ensure that oil, hydraulic fluid, and other fluids are at appropriate levels. Low levels can lead to equipment damage or failure.
- Evaluating Wear and Tear: Inspect critical components for signs of wear and tear, such as drill bits, hoses, and cables. Address any worn or damaged parts promptly.
Routine and Preventive Maintenance Tips for Drilling Rig Equipment
Routine and preventive maintenance tasks are essential for maximizing drilling rig performance and avoiding unexpected failures. The following tips should be incorporated into your maintenance program:
- Replacing Filters: Regularly replace filters as recommended by the manufacturer to maintain clean fluids and prevent equipment damage due to contamination.
- Lubricating Joints: Apply lubrication to the rig’s moving parts, such as joints and bearings, to reduce friction, minimize wear, and extend their lifespan.
- Addressing Wear and Tear: Conduct routine inspections to identify signs of wear and tear in critical components. Promptly address any issues by repairing or replacing worn-out parts to prevent failures during operations.
Effective Cleaning and Storage of Drilling Rigs
Proper cleaning and storage procedures are crucial for maintaining drilling rig equipment in optimal condition. Follow these tips to ensure equipment longevity:
Cleaning Procedures: Clean all components thoroughly after each use to remove mud, dirt, and debris. Use appropriate cleaning agents and techniques for different surfaces and materials.
Storage Guidelines: Store the drilling rig and its components in a clean, dry, and secure location. Protect the equipment from harsh weather conditions, unauthorized access, and potential damage.
Documentation: The Backbone of Efficient Maintenance
Maintaining comprehensive documentation of maintenance activities is vital for efficient drilling rig maintenance. Creating and maintaining a practical maintenance logbook can help you:
Record Keeping: Keep a detailed record of maintenance tasks performed, including dates, observations, and any issues encountered.
Organizational Tips: Organize the logbook in a structured manner, making it easy to navigate and retrieve information when needed.
Navigating Common Drilling Rig Maintenance Issues
Even with regular maintenance, certain issues may arise in drilling rigs. Being aware of these common maintenance issues and knowing how to address them can help minimize downtime and ensure the safety of personnel. Some common issues include:
- Hydraulic System Leaks: Identify and address hydraulic leaks promptly to prevent fluid loss and maintain system integrity.
- Electrical System Malfunctions: Troubleshoot and rectify electrical issues such as faulty wiring, loose connections, or malfunctioning control panels.
- Equipment Vibrations: Investigate and resolve excessive vibrations in the rig’s components, which can indicate misalignment, wear, or other mechanical issues.
Implementing a Preventive Maintenance Program for Drilling Rigs
Implementing a preventive maintenance program can significantly enhance the reliability and longevity of drilling rig equipment. Key elements of a successful program include:
Planning and Scheduling: Proactively plan and schedule maintenance tasks based on equipment specifications and manufacturers’ recommendations.
Staff Training: Train personnel on maintenance procedures, safety protocols, and the importance of adherence to preventive maintenance schedules.
Documentation and Evaluation: Maintain detailed records of maintenance activities and periodically evaluate the program’s effectiveness to identify areas for improvement.
Safety Considerations in Drilling Rig Maintenance
Safety should always be prioritized during drilling rig maintenance activities. Cultivating a safety-oriented culture and following established safety protocols contribute to better maintenance outcomes and minimize accidents. Consider the following safety considerations:
Safety Protocols: Develop and implement clear safety protocols for maintenance activities, including the use of personal protective equipment (PPE), lockout/tagout procedures, and working at heights guidelines.
Regular Safety Training: Conduct regular safety training sessions to educate personnel on potential hazards, safe practices, and emergency procedures.
Introducing FieldInsight for Drilling Rig Maintenance
When it comes to drilling rig maintenance management, FieldInsight stands out as a reliable and versatile software solution. With its extensive range of features and a focus on drilling rig maintenance, FieldInsight offers the flexibility, customizability, and scalability that drilling rig operators require to streamline their maintenance processes and ensure optimal performance.
- Scheduling: Effectively plan and schedule maintenance tasks for drilling rigs, ensuring that routine checks, preventive maintenance, and repairs are conducted in a timely manner. This helps minimize downtime and maximize operational efficiency.
- Inventory Management: Keep track of spare parts, tools, and supplies needed for drilling rig maintenance. FieldInsight enables efficient inventory management, ensuring that necessary items are available when required and minimizing delays in maintenance activities.
- GPS Tracking: Track the location of drilling rigs and associated equipment in real-time. This feature enhances visibility and allows for better coordination of maintenance activities, optimizing resource allocation and response times.
- Invoicing: Generate professional invoices for maintenance services rendered, making it easy to manage billing processes and ensure timely payment for maintenance work performed on drilling rigs.
- And More!
FieldInsight is committed to the success of its customers. From seamless implementation to dedicated support, the FieldInsight team is there to assist with any queries or concerns. Regular updates and continuous improvement ensure that the software evolves to meet the changing needs of drilling rig maintenance management.
Make the transition to FieldInsight and experience a hassle-free, all-in-one platform that caters specifically to drilling rig maintenance. With FieldInsight, you can streamline your maintenance processes, enhance productivity, and ensure the optimal performance of your drilling rigs.
Conclusion
Adhering to daily maintenance checks, conducting routine inspections, replacing filters, lubricating joints, and addressing wear and tear are vital steps in keeping drilling rig components in top condition. Additionally, effective cleaning and proper storage techniques help prevent corrosion, premature wear, and other potential issues.
Documenting maintenance activities in a practical logbook allows for better organization, easy reference, and effective analysis of maintenance data. It enables proactive decision-making and optimization of maintenance schedules and procedures.
By being aware of common maintenance issues and knowing how to address them, operators can quickly resolve problems and minimize operational disruptions. However, it is essential to prioritize safety during maintenance activities, establish clear safety protocols, and cultivate a safety-oriented culture to protect personnel and equipment.
Stay ahead of the curve in drilling rig maintenance management with FieldInsight. Empower your team, optimize maintenance schedules, and minimize downtime.
Schedule a demo or reach out to our team today to discover how FieldInsight can revolutionize your drilling rig maintenance practices. Gain features from scheduled maintenance tracking for preventative maintenance, to automated reporting. Find out how FieldInsight can help you today.
What You Should Do Now
- Book a Demo. You’ll be in touch with an automation expert who has worked in this space for over 5 years, and knows the optimal workflow to address your needs.
- If you’d like access to free articles about managing HVAC workflows, go to our blog.
- If you know someone who’d enjoy reading this page, share it with them via email, Linkedin, Twitter, or Facebook.