The Ultimate Guide to Preventative Maintenance for Fire Safety Assets
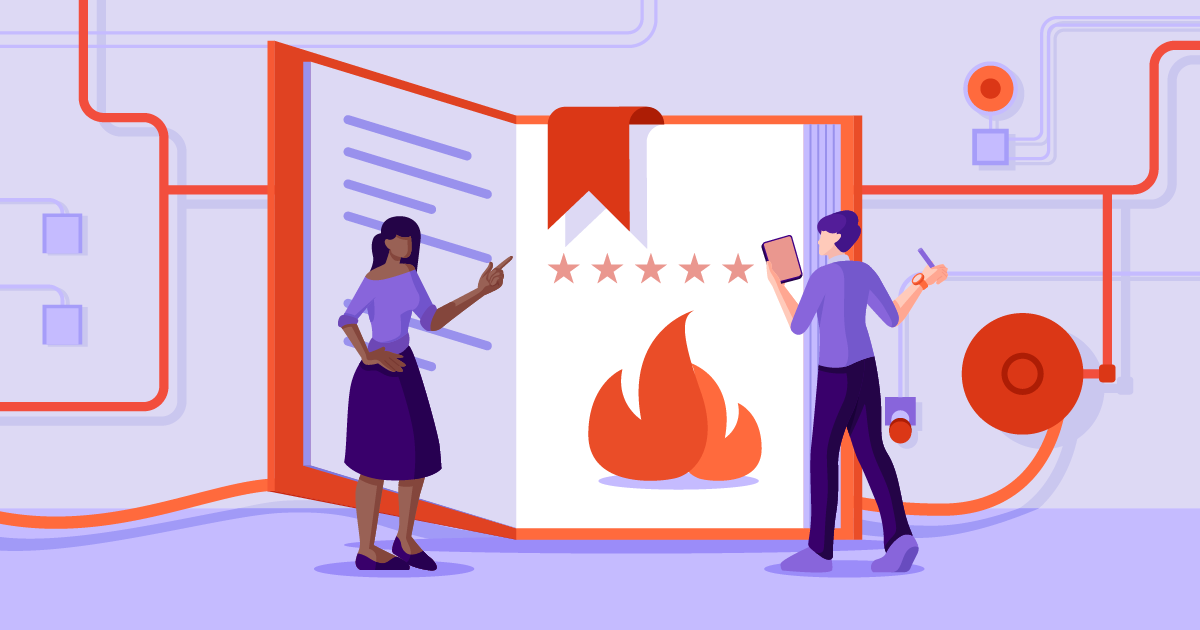
In the world of fire safety, the reliability of fire suppression systems, alarms, and other safety assets is non-negotiable. Preventative maintenance isn’t just routine care—it’s a critical safeguard against potential disasters. Across sectors, including Fire and Safety Australia, maintaining operational readiness of these systems is paramount to ensure they perform flawlessly during emergencies.
This guide explores how integrating advanced field service management software into asset maintenance practices can significantly enhance these essential operations. By adopting sophisticated preventative maintenance strategies, businesses can ensure that their fire safety assets are always ready when it matters most.
In this blog, you will learn about the transformative effects of technology on preventative maintenance, from setting up efficient maintenance schedules to leveraging predictive analytics for preemptive repairs. This guide provides invaluable insights into maintaining critical safety systems, detailing how to employ the latest technological innovations for optimal performance.
Understanding how to effectively implement these technologies is crucial.
In the high-stakes world of fire safety, the cost of equipment failure can be catastrophic. By enhancing the reliability of your safety assets and optimizing operational efficiency, you position your business to better manage potential risks and maintain compliance with stringent safety regulations. Equip yourself with the knowledge to stay ahead of equipment issues and ensure your systems are always prepared with the insights from this ultimate guide.
What is Preventative Maintenance?
Building on the crucial role of technology in enhancing fire safety operations, preventative maintenance stands as the cornerstone of ensuring that all safety measures function optimally.
But what exactly does preventative maintenance entail?
Simply put, it involves the systematic inspection, detection, correction, and prevention of potential failures before they occur. This proactive approach is essential in managing fire safety assets, where the cost of failure can be immeasurable.
For critical equipment such as fire extinguishers, smoke detectors, and sprinkler systems, preventative maintenance ensures these devices are not only compliant with the highest standards but are also ready to perform effectively when needed most. Regular checks and servicing, facilitated by advanced field service management software, allow businesses to schedule maintenance activities efficiently and track them meticulously, ensuring no component is overlooked.
Incorporating safety training as part of preventative maintenance routines also plays a pivotal role. Training ensures that personnel are equipped with the necessary knowledge to operate and maintain fire safety equipment correctly. This training, combined with the regular maintenance schedule, forms a robust defense against potential safety failures.
Field service management software enhances these processes by providing tools that manage schedules, document inspections, and ensure all maintenance activities are performed to the highest standards. By leveraging these digital tools, businesses can maintain a comprehensive log of maintenance records, making it easier to predict when equipment will need servicing and to prepare for inspections and audits.
Thus, preventative maintenance is not just about fulfilling a checklist; it’s about creating a culture of safety and reliability that permeates every aspect of an organization. By adopting proactive maintenance strategies and integrating the right technological tools, businesses can ensure their fire safety systems are always in peak condition, ready to protect lives and property.
Benefits of Regular Maintenance
Cost Efficiency Regular maintenance is not merely a routine chore; it’s a critical investment in the longevity and reliability of fire safety equipment. By adhering to a consistent maintenance schedule, businesses can avoid the exorbitant costs associated with equipment failures and emergency repairs.
Implementing workflow optimization procedures in the maintenance process ensures that resources are used efficiently, minimizing downtime and reducing expenses related to corrective actions. This strategic approach allows businesses to allocate their financial resources more effectively, enhancing overall operational cost-efficiency.
Asset Longevity The longevity of fire safety assets is crucial, especially considering the significant investment they represent. Well-maintained equipment not only functions more reliably but also lasts considerably longer, maximizing the return on investment.
Regular checks and upkeep prevent the wear and tear that can lead to premature breakdowns, thereby extending the useful life of these critical assets. Through diligent maintenance, businesses ensure that these assets continue to serve their protective purposes far beyond their expected lifespan.
Regulatory Compliance and Safety In industries dealing with fire safety and potentially hazardous materials, adhering to safety standards is paramount. Regular maintenance is essential, not just for adhering to these standards but for ensuring that all environments are truly safe.
Each location has specific regulatory requirements that dictate how often and in what manner safety equipment should be maintained. By establishing clear maintenance responsibilities and following prescribed procedures, businesses can ensure that their equipment meets all legal standards and operates effectively in critical situations. Regular maintenance checks provide documentation and evidence of compliance, which is vital during inspections and audits.
Through these practices, businesses not only maintain operational effectiveness but also uphold their responsibility to protect both people and property. Regular maintenance is a cornerstone of safety, ensuring that equipment functions as intended and that all preventive measures are in place to handle emergencies. This proactive approach not only fosters a safer workplace but also instills confidence among stakeholders that safety is a top priority.
Challenges in Preventative Maintenance
Preventative maintenance, crucial in ensuring the reliability of emergency services’ equipment, faces numerous operational hurdles. One significant challenge is the effective tracking and management of the maintenance needs of a diverse array of assets. In the fire & safety industry, where the accuracy of metric and imperial units can mean the difference between functionality and failure, reliance on manual methods can be particularly precarious.
Manual tracking systems are not only labor-intensive but also highly susceptible to human error. In scenarios where a fire starts, even a minor oversight in maintaining critical equipment can lead to catastrophic consequences, including substantial property damage and severe public safety risks. The stakes in maintaining and inspecting fire safety apparatus demand precision and consistency that manual systems often fail to deliver.
Moreover, traditional methods lack the immediacy required to take action immediately when issues are detected. In a field where every second counts, especially during emergency responses, delays caused by inefficient maintenance processes can hinder the effectiveness of fire safety operations, putting lives and properties at even greater risk.
Transitioning from these outdated practices to more sophisticated, technology-driven systems can mitigate these risks significantly. Implementing advanced field service management software that can automate and streamline maintenance schedules ensures no asset is overlooked and maintenance actions are prompted and recorded accurately. This not only enhances the efficiency of maintenance operations but also fortifies the safety protocols critical to effective fire and emergency services.
The Role of Technology in Maintenance
The advent of innovative technologies such as the Internet of Things (IoT) and Artificial Intelligence (AI) has revolutionized the approach to maintenance in the fire service sector. No longer just a reactive task, maintenance has evolved into a proactive, strategic operation critical to ensuring the readiness and reliability of fire safety equipment. These technologies are at the heart of modern field service management software systems, like FieldInsight, which are designed to streamline and enhance maintenance operations for fire service companies.
IoT in Maintenance: IoT technology has transformed maintenance by enabling continuous monitoring of equipment performance. Sensors embedded in fire safety equipment can detect and report in real time any deviation or malfunction that could indicate a potential failure. This capability allows fire services to respond immediately, often before a breakdown occurs, which can prevent dangerous lapses in fire protection readiness.
AI and Predictive Maintenance: AI leverages data collected from IoT devices to predict when equipment might fail or when it will need servicing. By analyzing trends and usage patterns, AI algorithms can forecast potential issues and automatically schedule maintenance tasks, ensuring that they are carried out without delay. This predictive approach minimizes the risk of unexpected equipment failures and enhances the efficiency of maintenance operations.
Integration with Field Service Management Software: Field service management software, such as FieldInsight, plays a crucial role in integrating these technologies into a cohesive system. FieldInsight, updated regularly to incorporate the latest technological advances, provides a platform where all data and maintenance activities are centralized. The software ensures that maintenance schedules are automatically updated based on AI predictions and IoT alerts, allowing fire service companies to maintain a proactive stance on equipment upkeep.
Benefits of Technology-Enhanced Maintenance: The integration of IoT and AI into field service management software like FieldInsight enables fire service companies to operate more efficiently. Automatic updates and alerts help avoid the downtime associated with manual tracking and scheduling, ensuring that all maintenance activities are timely and that no equipment is overlooked. This not only boosts the operational capacity of fire services but also significantly reduces the risk associated with outdated or malfunctioning equipment, enhancing overall public safety.
By adopting technologies that allow for predictive maintenance and automatic updates, companies in the fire service industry can ensure their equipment operates reliably and efficiently, safeguarding both their assets and the communities they serve.
Choosing the Right Field Service Software
Selecting the optimal field service management software is crucial for enhancing operational efficiencies, particularly in preventive and asset maintenance within the fire safety sector. A well-chosen software solution streamlines complex processes and ensures that fire safety assets are maintained to the highest standards. Here are the key features to look for:
Automate Maintenance Scheduling: The software should be capable of automating the scheduling of maintenance tasks to ensure there are no lapses in maintenance activity. Automated scheduling helps prevent the human error associated with manual entry and ensures that all preventive maintenance activities are conducted on time, without fail. This automation is essential for maintaining the operational readiness of critical fire safety equipment, thereby enhancing overall safety and reliability.
Comprehensive Asset Tracking: Effective field service management software provides robust asset tracking capabilities. It should offer a detailed overview of every asset, including its maintenance history, current status, and future maintenance requirements. This level of detail is crucial for fire safety, where each piece of equipment must function flawlessly in an emergency. Asset tracking supports proactive maintenance strategies and helps fire safety companies manage their resources more effectively, ensuring that all assets are accounted for and maintained.
Mobile Access for On-the-Go Updates: Mobile access is another critical feature. Technicians in the field need real-time access to maintenance schedules, asset information, and other critical data. Mobile functionality enables on-site technicians to receive updates, report issues immediately, and access necessary documents without needing to return to the office. This capability ensures that all team members are informed and can react swiftly to any changes or requirements, thereby enhancing the efficiency of maintenance operations.
Detailed Reporting for Compliance and Auditing: The software should also offer detailed reporting features that assist in compliance and auditing processes. Fire safety regulations are stringent, and having accurate, up-to-date records is essential for passing inspections and audits with ease. Detailed reports generated by the software should cover all aspects of maintenance and compliance, providing clear evidence that all regulations are being met and that every asset is maintained according to the required standards.
By ensuring that your field service management software includes these features—automate maintenance scheduling, comprehensive asset tracking, mobile access, and detailed compliance reporting—fire safety organizations can significantly enhance their operational efficiency. More importantly, they can ensure that all preventive maintenance and asset maintenance tasks are performed flawlessly, thereby safeguarding assets and ultimately protecting lives.
How Field Service Software Enhances Preventative Maintenance
Streamlined Scheduling: Automated systems ensure maintenance is never overlooked, with scheduled reminders and checklists. Real-Time Data Access: Mobile apps allow instant updates from any location, improving response times and accuracy. Asset History Analysis: Data analytics provide insights into the performance and maintenance history of each asset, enabling better decision-making.
Steps to Implement Field Service Software
- Evaluate Your Needs: Understand what specific functionalities your operations require from software.
- Software Selection: Choose software that aligns with your operational needs and budget.
- Integration and Training: Ensure the software integrates smoothly with your current systems and provide comprehensive training to all users.
- Continuous Improvement: Use feedback and software analytics to continually refine and improve your maintenance processes.
Future Trends in Maintenance Technology
As we look toward the future, the field of preventative maintenance in the fire service is set to embrace significant technological advancements. With the adoption of more sophisticated predictive analytics, emergency response teams will be better equipped to anticipate and mitigate potential failures before they escalate into current incidents. The integration of Artificial Intelligence (AI) will streamline routine maintenance tasks, improving efficiency and accuracy in real-time operations. Furthermore, an expanded use of Internet of Things (IoT) sensors will enhance the monitoring of fire safety equipment, providing continuous data that helps in making informed decisions during critical moments.
Safeguarding Lives with Cutting-Edge Maintenance Solutions
In the critical world of fire safety, complacency is never an option. By harnessing the power of advanced field service management software like FieldInsight, you can revolutionize your preventative maintenance practices, ensuring your fire safety assets are always operating at peak efficiency. Don’t let outdated methods or manual processes compromise your readiness – book a demo with FieldInsight today and experience firsthand how our cutting-edge solutions can streamline your maintenance operations, enhance asset longevity, and fortify your commitment to safety.
Our experts will guide you through the seamless integration of predictive analytics, IoT sensors, and AI-driven automation, empowering you to stay ahead of potential failures and safeguard lives and property. Embrace the future of preventative maintenance and take the first step towards unparalleled safety and operational excellence. Book your demo now and unlock the full potential of your fire safety assets.
What You Should Do Now
- Book a Demo. You’ll be in touch with an automation expert who has worked in this space for over 5 years, and knows the optimal workflow to address your needs.
- If you’d like access to free articles about managing HVAC workflows, go to our blog.
- If you know someone who’d enjoy reading this page, share it with them via email, Linkedin, Twitter, or Facebook.