Free Heavy Equipment Preventive Maintenance Checklist (Template) For Commercial Businesses
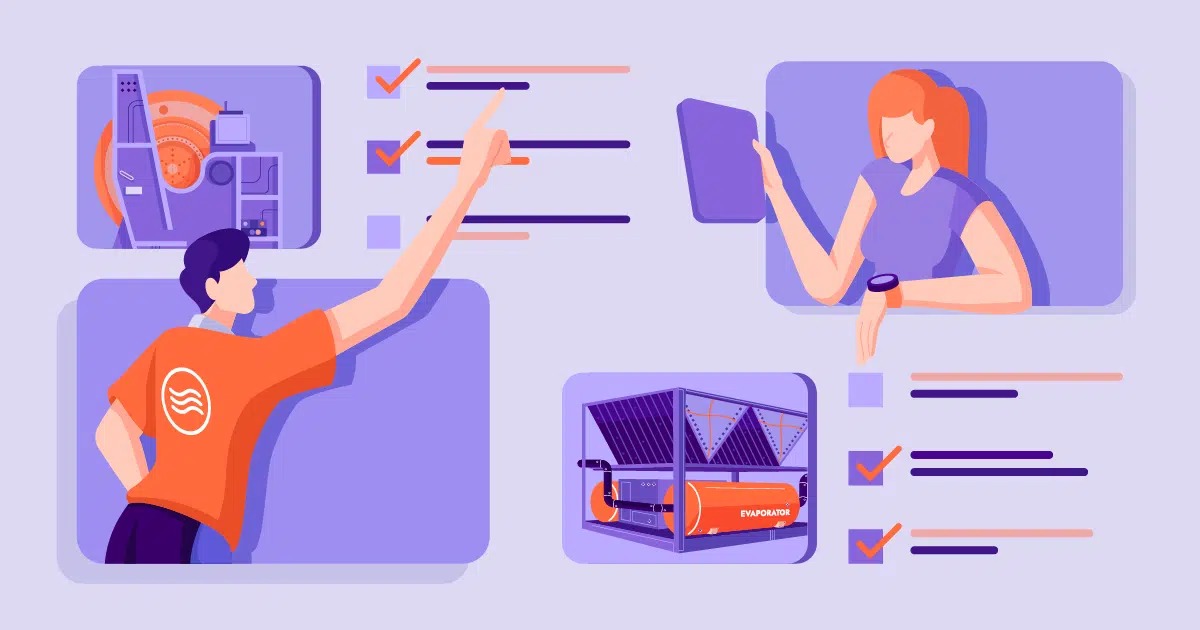
We all know that construction and commercial equipment gets its fair share of use on the job site. But does your equipment get the right preventive maintenance that its hard work has earned?
Equipment operations costs can become expensive, especially when your equipment isn’t well maintained and you have constant breakdown cost repairs. HVAC maintenance is vital in any commercial business to reduce repair costs, reduce equipment breakdown and prolong equipment life span.
The best way to ensure your equipment maintenance stays on track is with a great checklist or template in your job management process. Do you have the right equipment maintenance measures in place for your business? Or are your assets in the fast lane towards equipment failure? In this article we will break down how you can improve your heavy equipment maintenance schedule in just a few easy steps.
What is heavy equipment maintenance?
Heavy equipment maintenance includes the visual inspections and servicing of assets according to a maintenance plan. With a maintenance program you can develop a schedule for your service tasks that will better help you in the future to predict trends in your assets. Heavy equipment maintenance is usually performed according to a manufacturer’s recommendations and frequencies. Equipment maintenance can include anything as small as cleaning a site or as significant as replacing parts. The benefits of regular maintenance can easily boost equipment longevity and reduce the chance of sudden component failure.
Example of pre-start checks
There is a lot that is involved with heavy equipment maintenance and it can begin before you even touch an asset. A typical pre-start checklist can include:
- Practice safe parking
- Check that you have the tools and equipment you need
- Check surrounding area for hazards
- Inspect for leaks, signs of rust or contamination
- Insect tyres
- Check for leaks on the ground
- Check battery
- Check electrical wires and components
- Inspect the underside of the asset
Your pre-start checklist will include mostly a visual inspection to ensure that the asset is safe to begin maintenance on.
Example of a heavy equipment preventative maintenance checklist
For your heavy equipment checklist, there are some vital parts that you will need to include in your next inspection.
Primary components
- Inspect exhaust
- Check tyres for tread wear
- Check wheel alignment
- Insect steering
- Inspect tracks
Engine checks
- Inspect battery
- Check coolant levels
- Inspect belt
- Check oil levels
- Inspect filter
- Check hose for leaks
Cab and dashboard
- Check condition of steps and safety bar
- Check door seal
- Test lights in cab and headlights
- Test wipers
- Check for engine lights
Top 6 factors you should include in your preventive maintenance program for heavy equipment
For smooth operation in your routine maintenance, you will need to know the specific requirements for your heavy equipment. For the best equipment maintenance results here are the top factors you should include in your preventative maintenance plan:
1. Create a heavy equipment maintenance checklist
Your maintenance plan can include more than one type of checklist. You may find that you have daily checklists, monthly checklists, pre-start checklists, shutdown checklists and checklists based on usage. Your regular maintenance checklist should always be constructed based on your equipment manual directions.
For your every 500 hours usage checklist, you might find your construction equipment checklist looks like:
- Check for leaking hydraulic lines
- Inspect hydraulic oil level
- Check hydraulic system
- Replace hydraulic filters
- Check engine coolant levels
- Check engine oil
- Inspect belt driven components
- Fluid analysis
- Check electrical lines
- Check fuel delivery system
- Inspect fuel lines
- Check brake lights including parking brake
- Insect valve stems
- Inspect economical operation of asset
- Assess voltage retention
- Visual inspection of lift arms
- Check battery’s age
- Update service records with results
A typical daily shutdown checklist might include:
- Top up fuel tank
- Inspect fluid levels
- Check safety devices
- Park equipment in secure place
- Clean up site
For ease of use, you want your checklist to be structured in such a way that it is easy for your technicians to follow. Usually checklists will begin at the ground and work upwards. For the best practices for equipment maintenance, you should use your maintenance history and service records to build your checklists and determine the highest priorities.
2. Know your common breakdown causes
To help with predicting maintenance issues in your business, the best thing to do is look to the past. Poor maintenance plans are usually the result of a lack of knowledge. As you build your preventive maintenance program, you will need to make adjustments. You might not get your maintenance plan right the first time and a little tweaking might be needed. Your future maintenance will benefit from this.
There are three types of heavy equipment and construction equipment breakdowns that your causes might fit into:
- Sudden failure
- Intermittent failure
- Gradual failure
Your equipment failure could be caused from mechanical, thermal, electrical or erratic causes. One of the biggest maintenance tips is learning from your mistakes and including preventative steps in your maintenance that reflect common breakdown causes.
3. Have a thorough asset knowledge
For your heavy equipment maintenance schedule, you need to have the right knowledge in your team if you want to succeed. One of the benefits of preventive maintenance is that you probably have a lot more information that you think in your team. You will find that your equipment management will hugely benefit from listening to your machine operators. These team members as well as your equipment manual will both help you construct a knowledge base for your equipment. When you know your equipment, you can easily identify key problems and predict trends.
4. Have a well trained maintenance team
Another key step to ensuring that your routine preventive maintenance is beneficial, is having well trained machine operators. With well trained operators, you can ensure they follow safety requirements and help reduce costly repairs.
You might find that you need to have routine preventive maintenance training sessions to keep your team up to date with regular maintenance plans. Some form of training should be delivered for following maintenance tips, scheduling regular maintenance and ticking off checklists. Training doesn’t have to be a lengthy process and can involve reviewing the equipment manual and processes.
5. Know your manufacturer’s recommendations
For your preventative maintenance program, you should closely follow the manufacturer’s recommendations to reduce the chance of voiding warranty claims or SLAs. You should use your equipment manual as a guide to schedule your heavy equipment frequencies and maintenance intervals. Your required maintenance procedures will also detail any technical monitoring or reporting requirements. To reduce any unexpected repair costs, the manufacturer will often have an outline for what should be included in your maintenance checklist.
6. Have a great documentation process
You might have a well trained team, a great PM schedule and checklists, but if you don’t have somewhere safe to store your equipment information, you will find yourself running in circles. In this day and age, pen and paper have become redundant in the field service and commercial industries. To create smooth operations, you need an automated software that is accessible from both the office and the field. When you have the power to store and access asset history and checklists from the field, you save time and create an investment in your business.
The importance of the preventive maintenance template
Now you know what your preventive maintenance plan should include, you need to build your template. Templates for construction equipment are vital when working in a high risk industry. With the risk of hazards on every site, a template can help reduce the risk of accidents and incorrect procedures in the workplace. Here are the top reasons why a template is essential to your business.
1. Create job productivity and consistency
With a heavy equipment preventive maintenance plan, you can easily create a sense of consistency in your business. Your checklist will ensure that your technicians are keeping up peak performance while in the field and significantly increasing productivity.
Preventive maintenance programs easily outline steps for your technician to follow and reduce the chance of something going wrong or being missed. Heavy equipment maintenance checklists will also help in training new employees as you will have simple steps to help them do the job right. With checklists you will find that the overall quality of your work will increase as a result.
2. Reduce costly repairs
With daily, monthly and annual preventive maintenance, you will significantly reduce operating costs and eliminate waste in your business. Unlike emergency breakdowns, preventive maintenance will be a repetition and easily allow you to predict necessary spare parts and resources needed. With the assistance of a checklist, this reduces the amount of downtime and operating costs that go into unplanned breakdowns.
3. Boost safety in your business
Having a template for your heavy equipment routine maintenance will also boost safety in your workplace. Checklists and templates will typically entail required PPE and risk assessments for your job. By following these steps, you can ensure that your technicians are always keeping safe while on site.
Want to find out what happens when you don’t have a good safety template in place? See the 9 Construction Accident & Safety Statistics in 2021 you should know about.
4. Less unexpected issues
When you use a maintenance checklist in your business, you significantly reduce the chance that something will happen outside your scope of work. Your checklist is designed to reduce unplanned equipment downtime and far fewer breakdowns will occur as a result. You will find that your troubleshooting becomes more simple as you will have the benefit of your checklist to ensure that the correct procedures have been followed.
Key takeaways for proper maintenance
The key takeaways that you need to remember:
- Checklists are important to reducing operating costs and boosting equipment longevity
- Know your equipment
- Train your maintenance team
- Store your equipment maintenance history
The best way to tick all these requirements is to have a great preventive maintenance software in your business. To ensure that your heavy equipment maintenance is successful, you need a system that can track your inventory, keep tabs on your team, store valuable asset data, update SWMS in the field and have easy to follow checklists.
FieldInsight is the all-in-one software that can boost your preventive maintenance program to the next level. Don’t struggle with cumbersome paper based systems and double data entries. Your PM plan should be easy to follow and accessible from both the office and the field. Get your team on the right track and get started by booking a demo today.
What You Should Do Now
- Book a Demo. You’ll be in touch with an automation expert who has worked in this space for over 5 years, and knows the optimal workflow to address your needs.
- If you’d like access to free articles about managing HVAC workflows, go to our blog.
- If you know someone who’d enjoy reading this page, share it with them via email, Linkedin, Twitter, or Facebook.