Overcoming Equipment Maintenance Challenges: A Comprehensive Guide
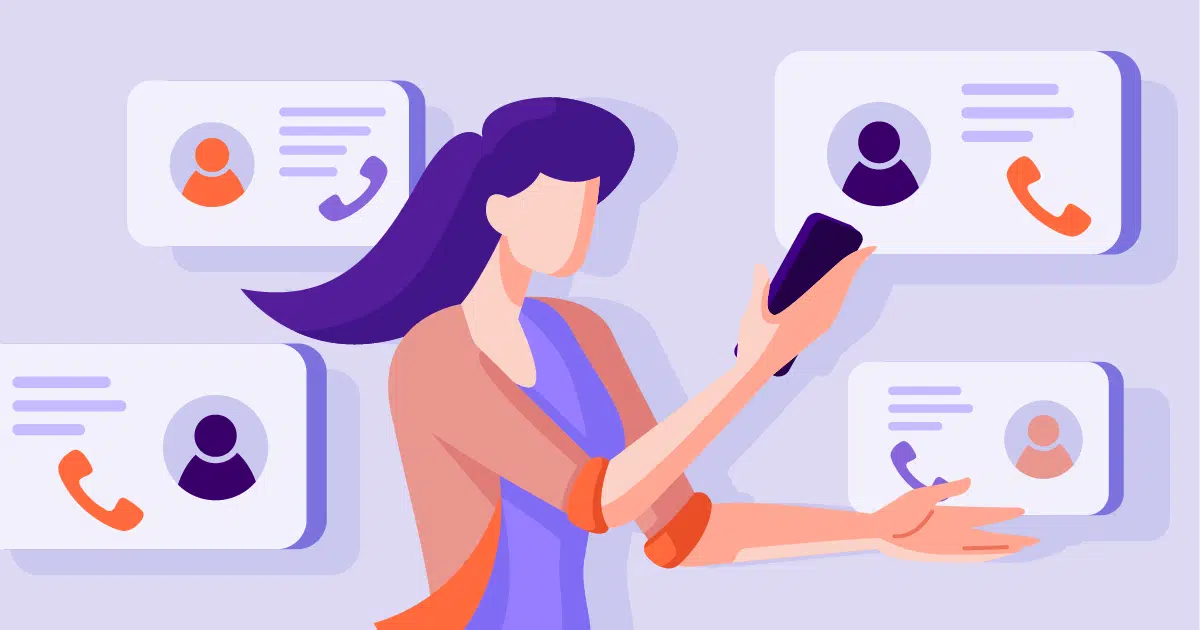
In today’s dynamic industrial landscape, the seamless functioning of equipment is not just a matter of operational efficiency; it’s a fundamental driver of productivity and profitability. Equipment maintenance plays a pivotal role in this equation. It’s not merely a reactive task but a proactive strategy that can significantly impact the bottom line. In this comprehensive guide, we will explore the intricate world of equipment maintenance, the challenges it poses, and how FieldInsight’s integrated asset management platform emerges as a game-changing solution, simplifying tasks, and streamlining processes.
The Crucial Role of Equipment Maintenance
Industries worldwide rely on an extensive array of equipment to execute their processes efficiently. Whether it’s heavy machinery on a construction site, precision instruments in a laboratory, or a fleet of vehicles for logistics, the reliability and performance of these assets are paramount. Without effective maintenance, the very foundation of these industries can crumble.
Prolonging Equipment Lifespan: The correlation between regular maintenance and prolonged equipment lifespan cannot be overstated. A well-maintained machine can serve its purpose far beyond its expected lifespan, saving organizations substantial capital in the long run.
Costly Consequences of Neglect: Neglecting maintenance can lead to costly consequences. Unplanned breakdowns, emergency repairs, and the need for premature equipment replacements are just a few of the financial burdens that result from neglecting routine maintenance.
FieldInsight’s Solution: FieldInsight offers a comprehensive solution to these challenges. Their integrated asset management platform empowers industries to proactively address equipment maintenance, ensuring smooth operations and cost-effective asset management.
Understanding Equipment Maintenance Challenges
A Wide Array of Equipment
Across various industries, equipment comes in a vast array of forms, from heavy machinery to intricate electronic components. Each of these serves a unique purpose, and as a result, each has its own set of maintenance requirements. Understanding the distinct needs of different types of equipment is paramount to effective maintenance.
Diverse Maintenance Needs: Heavy machinery, for instance, may require regular lubrication, while electronics demand delicate calibration. The one-size-fits-all approach simply doesn’t work in the realm of equipment maintenance.
Expertise Matters: Maintaining such diverse equipment necessitates a high level of expertise. Maintenance teams must possess a deep understanding of the intricacies of each machine and be well-versed in the specific maintenance procedures required.
Maintenance Complexity
The world of maintenance is far from one-size-fits-all. Maintaining different types of equipment can be a complex endeavor, involving a multitude of procedures. Each piece demands specific attention and expertise, making maintenance a multifaceted challenge.
Varied Maintenance Procedures: Some equipment may require routine inspections and lubrication, while others demand more involved processes like component replacements and calibration. Keeping track of these varied procedures can be a logistical challenge.
Resource Allocation: Properly allocating resources, both in terms of personnel and materials, is crucial. Maintenance teams must juggle resources efficiently while considering budget constraints and minimizing downtime.
Resource Management
Ensuring that the right resources, tools, and skilled personnel are available for maintenance tasks is a constant juggling act. The allocation of these resources must be carefully managed, often complicated by budget constraints and scheduling conflicts.
Resource Availability: Availability of critical resources, from spare parts to skilled technicians, is pivotal. Running out of essential parts or not having the right expertise on hand can lead to costly delays.
Budget Constraints: Organizations often operate within budget constraints, necessitating careful resource allocation. This balance between maintaining equipment effectively and managing costs can be challenging to achieve.
Compliance and Safety
Maintenance isn’t just about keeping equipment running; it’s about doing so in a manner that adheres to stringent safety standards and regulations. Failure to do so not only poses risks to personnel but also exposes the organization to potential legal and financial repercussions.
Safety Standards: Different industries have specific safety standards and regulations that must be adhered to during maintenance activities. Non-compliance can lead to accidents, injuries, and costly legal penalties.
Protecting Personnel: Prioritizing safety is not just a matter of compliance; it’s a moral imperative. Safety protocols and training are essential to protect maintenance personnel from harm during their work.
Protecting Equipment: Safety measures also extend to protecting the equipment being serviced. Mishandling or improper maintenance procedures can damage valuable assets, leading to costly repairs or replacements.
Common Equipment Maintenance Challenges
Maintenance Scheduling
Balancing maintenance schedules with operational needs can be likened to solving a complex puzzle. It requires meticulous planning to ensure that maintenance activities do not disrupt ongoing operations. Failing to strike this balance can lead to costly downtimes and disruptions.
Operational Continuity: Industries cannot afford to halt operations for maintenance indefinitely. Maintenance scheduling must consider peak production times, client commitments, and other operational priorities.
Preventive vs. Reactive: Effective scheduling can mean the difference between preventive maintenance, which is planned and minimally disruptive, and reactive maintenance, which is often costly and chaotic.
Parts Availability
One of the most frustrating scenarios in maintenance is needing a critical spare part and discovering that it is unavailable. The challenges of sourcing and managing spare parts can result in significant delays and increased costs.
Just-in-Time vs. Stockpiling: Organizations must strike a balance between just-in-time part procurement, which minimizes inventory costs, and stockpiling critical parts, which ensures they are readily available when needed.
Supplier Reliability: Relying on external suppliers for parts introduces another layer of complexity. Ensuring the reliability and timely delivery of parts is essential to avoid disruptions.
Unpredicted Breakdowns
Sudden equipment failures can have far-reaching consequences. They can disrupt production schedules, increase maintenance costs, and damage a company’s reputation. Developing strategies to preempt these disruptions is not just important; it’s essential.
The Cost of Downtime: Unplanned equipment downtime can be extraordinarily expensive, not only in terms of immediate repair costs but also in terms of lost revenue and productivity.
Predictive Maintenance: The advent of predictive maintenance technologies has revolutionized the field by enabling organizations to anticipate equipment failures and perform maintenance proactively.
Quality Assurance
To ensure that equipment continues to perform optimally, maintenance activities must not only meet but often exceed industry standards. Maintaining the highest level of quality is critical to ensuring that equipment operates safely and efficiently.
Industry Standards: Industries often have specific standards and best practices that govern maintenance procedures. Striving to meet or exceed these standards is crucial for compliance and performance.
Performance Metrics: Establishing performance metrics and continuously monitoring them is essential for quality assurance. Metrics can include equipment uptime, failure rates, and the effectiveness of maintenance activities.
Leveraging Technology for Efficient Maintenance
Digital Maintenance Logs
One of the most significant advancements in the field of maintenance is the adoption of digital maintenance logs. These software tools offer numerous advantages, including streamlined tracking and scheduling of maintenance activities. Digital logs provide transparency and efficiency like never before, allowing maintenance teams to manage tasks with greater precision and accuracy.
Transparency and Accessibility: Digital maintenance logs are accessible to authorized personnel from anywhere with an internet connection. This accessibility ensures that all team members are on the same page regarding maintenance activities.
Historical Data: Digital logs store historical maintenance data, facilitating trend analysis and decision-making. This data can help organizations identify patterns of equipment wear and tear, enabling more proactive maintenance.
Integration: Many digital maintenance log systems can integrate with other enterprise software, such as enterprise resource planning (ERP) systems. This integration streamlines data flow and enhances overall operational efficiency.
Equipment Health Monitoring
Predicting and preventing potential equipment failures is no longer a gamble. Technology has empowered us to take a proactive approach to maintenance through equipment health monitoring systems. These systems continuously collect data on equipment performance and can provide early warnings of impending issues, allowing maintenance teams to take corrective action before a breakdown occurs.
Continuous Data Collection: Equipment health monitoring systems gather data around the clock, providing a real-time view of equipment performance. This continuous data collection is essential for early issue detection.
Predictive Analytics: Advanced analytics tools can process the collected data to predict equipment failures before they occur. This proactive approach minimizes downtime and reduces maintenance costs.
Condition-Based Maintenance: Condition-based maintenance strategies rely on equipment health monitoring data to determine when maintenance is needed based on the actual condition of the equipment, rather than fixed schedules.
Real-time Alerts
In the fast-paced world of industrial maintenance, real-time alerts are indispensable. These notifications serve as early warning systems for critical maintenance tasks or issues. Whether it’s a sudden drop in equipment performance or a pending part replacement, real-time alerts enable maintenance teams to respond swiftly and address problems before they escalate.
Timely Intervention: Real-time alerts ensure that maintenance teams can intervene promptly, minimizing the impact of potential issues on operations.
Preventing Catastrophic Failures: By addressing issues at an early stage, organizations can often prevent catastrophic equipment failures that can result in costly repairs and downtime.
Remote Monitoring: Many modern maintenance systems offer remote monitoring capabilities, allowing teams to receive alerts and monitor equipment status from virtually anywhere.
Data-Driven Decisions
Analytics play a pivotal role in enhancing maintenance strategies. By analyzing data collected from equipment and maintenance activities, organizations can gain valuable insights into equipment performance and predict wear and tear more accurately. These data-driven decisions can lead to more efficient maintenance processes and cost savings in the long run.
Predictive Maintenance Models: Advanced predictive maintenance models use historical data to forecast when equipment is likely to fail. These models help organizations allocate maintenance resources more effectively.
Optimizing Maintenance Frequency: Data analysis can reveal patterns in equipment wear and tear, enabling organizations to optimize the frequency of maintenance activities to prevent issues without overburdening resources.
Cost Analysis: Data-driven decisions also extend to cost analysis, allowing organizations to evaluate the cost-effectiveness of different maintenance strategies and make informed choices.
Best Practices for Effective Equipment Maintenance
Regular Inspections
Routine inspections are the cornerstone of effective equipment maintenance. These regular checks are essential for identifying potential issues early, allowing maintenance teams to take proactive measures to prevent breakdowns and extend equipment life cycles.
Early Issue Detection: Regular inspections are designed to catch problems in their infancy, when they are easier and less expensive to address.
Preventive Maintenance: Inspections often lead to preventive maintenance activities, such as lubrication, adjustments, and minor repairs, that can significantly extend equipment life.
Checklists and Procedures: Establishing comprehensive checklists and maintenance procedures ensures that inspections are thorough and consistent.
Training and Development
Equipping maintenance personnel with the latest techniques and knowledge is crucial. Ongoing training and development programs ensure that maintenance teams stay up-to-date with industry best practices and the latest advancements in equipment technology. Well-trained teams are more capable of handling maintenance challenges effectively.
Continuous Learning: Maintenance is a dynamic field, with new technologies and techniques constantly emerging. Providing ongoing training ensures that maintenance personnel remain at the forefront of their profession.
Skill Diversification: Cross-training maintenance teams to work on different types of equipment enhances their versatility and adaptability.
Certifications: Encouraging maintenance personnel to pursue relevant certifications demonstrates a commitment to excellence and professionalism.
Safety First
Safety should always be a top priority during maintenance activities. Prioritizing safety not only protects personnel from harm but also safeguards the equipment being serviced. Mishandling or improper maintenance procedures can lead to accidents, injuries, and costly damage.
Safety Protocols: Establishing clear safety protocols and procedures for maintenance tasks is essential. These protocols should address potential hazards and outline safety measures.
Safety Equipment: Providing the necessary safety equipment and ensuring its proper use is critical. This includes personal protective equipment (PPE) such as gloves, helmets, and safety glasses.
Training and Awareness: Regular safety training and awareness programs help instill a culture of safety within maintenance teams, reducing the risk of accidents.
Documentation
Detailed documentation is essential for effective maintenance management. Maintaining records of all maintenance activities, including parts replaced, observations, and equipment conditions, serves as a roadmap for continuous improvement. It provides a historical record of maintenance efforts and can help identify trends and areas for optimization.
Maintenance Logs: Keeping meticulous maintenance logs provides a record of all activities performed on each piece of equipment. This log can be invaluable for troubleshooting and historical reference.
Parts Inventory: Maintaining an accurate inventory of spare parts, along with records of when parts were used, helps ensure that critical components are always available.
Performance Tracking: Documentation can also track equipment performance over time, allowing organizations to identify trends, patterns, and potential areas for improvement.
The Impact of Proactive Equipment Maintenance
Extended Equipment Lifespan
Perhaps the most tangible benefit of proactive equipment maintenance is the extension of equipment lifespans. Regular maintenance practices, including inspections, lubrication, and component replacements, can add years to the operational life of equipment. This not only protects the organization’s investment but also reduces the frequency of expensive equipment replacements.
Maximizing ROI: By prolonging the lifespan of equipment, proactive maintenance practices maximize the return on investment (ROI) for each asset.
Reduced Capital Expenditure: Organizations can reduce capital expenditures by avoiding premature equipment replacements, which can be a substantial financial burden.
Sustainability: Extending equipment lifespans aligns with sustainability goals by reducing the environmental impact associated with manufacturing and disposing of equipment.
Reactive Maintenance & Operational Efficiency
Well-maintained equipment is the cornerstone of operational efficiency. When equipment functions optimally, it contributes to consistent and efficient operations. Reduced downtime and fewer disruptions lead to smoother production processes and improved overall efficiency.
Consistency: Equipment that operates consistently and predictably contributes to a more stable production environment. This consistency is vital for meeting customer commitments and maintaining product quality.
Resource Optimization: Operational efficiency also extends to resource optimization. With fewer breakdowns and less downtime, resources can be allocated more effectively, improving overall cost efficiency.
Customer Satisfaction: Consistent operations and on-time deliveries contribute to enhanced customer satisfaction and retention.
Not only do you reduce equipment management challenges like unplanned downtime and excessive maintenance costs, you can better sync your maintenance team and keep up to date with the latest equipment construction industry trends- everything in your workflow becomes easier to manage when your not stressing about unplanned breakdowns and letting chaos rule your business.
Cost Savings And Equipment Failure
One of the most compelling reasons to embrace proactive maintenance is the potential for cost savings. Preventing major breakdowns through regular maintenance is far more cost-effective than reacting to unexpected failures. Maintenance costs are predictable and manageable, allowing organizations to allocate resources more efficiently and avoid the high costs associated with emergency repairs.
Predictable Maintenance Costs: Proactive maintenance strategies allow organizations to predict maintenance costs more accurately, making budgeting and financial planning more straightforward.
Reduced Emergency Costs: Emergency repairs, often necessitated by equipment breakdowns, can be significantly more expensive than planned maintenance activities. By preventing emergencies, organizations can reduce these costly occurrences.
Improved Resource Allocation: Proactive maintenance practices lead to better resource allocation. Organizations can assign personnel and materials more effectively, minimizing waste and maximizing value.
Key Takeaways for Maintenance Teams
In conclusion, proactive equipment maintenance is not just a necessity; it’s a strategic imperative for industries across the board. The correlation between consistent maintenance and the prolonged lifespan of equipment cannot be overstated. By embracing technology solutions like FieldInsight, organizations can take a holistic approach to equipment maintenance. FieldInsight’s integrated asset management platform simplifies tasks, streamlines processes, and empowers maintenance teams to excel.
Don’t wait for breakdowns to strike; instead, leverage the power of technology and proactive maintenance practices to stay ahead of challenges. In doing so, you not only ensure that your equipment performs optimally but also contribute to operational efficiency and cost savings that can transform your organization’s bottom line. Embrace proactive equipment maintenance as your competitive edge in an ever-evolving industrial landscape, and reap the rewards of sustained success.
As we delve deeper into the nuances of equipment maintenance and the transformative impact it can have on industries, we’ll explore specific examples, case studies, and actionable insights to empower your organization to navigate the complex landscape of equipment maintenance with confidence and competence. Stay tuned for a wealth of knowledge that will empower your maintenance teams and drive operational excellence.
What You Should Do Now
- Book a Demo. You’ll be in touch with an automation expert who has worked in this space for over 5 years, and knows the optimal workflow to address your needs.
- If you’d like access to free articles about managing HVAC workflows, go to our blog.
- If you know someone who’d enjoy reading this page, share it with them via email, Linkedin, Twitter, or Facebook.